Alan Mulder double checks the route on his tablet. “Are we going the right way?” the Lapp sales expert asks his colleague Ayanda Dayimani, who is at the wheel, and zooms in for a closer look at the map. The 41 year old nods. He knows the route. Lapp’s white van leaves the paved road of national route N14 a few kilometres after Vryburg, a small town with around 20,000 inhabitants in the North West province of South Africa, almost 400 kilometres west of Johannesburg. Dayimani drives the vehicle over the gravel and sand track. Time and again he swerves around deep potholes. Mulder’s tablet bounces on his lap. Curious ostriches on the edge of the road disappear in the swirling sand in the rear view mirror. The journey leads through the middle of the Kalahari thornveld, a mixture of vegetation made up of grassland and thicket, typical of northern South Africa.
“The road has always existed. If you keep going, you get to a town. That’s what people say at least. I’ve never been there,” grins Dayimani. After almost half an hour, he turns off. They have reached their destination: The construction site for a new solar park. Construction for the future is being carried out in the heart of the African wilderness, as it is in many other places on the continent. The use of renewable energies – especially from the sun – opens up opportunities for 600 million people who have previously had no access to electricity. That is half of the African population. Mulder and Dayimani climb out, take a hearty gulp of water, put on a helmet and safety vest – and are happy. This is because the drums with the solar cables from Lapp have already been delivered.
400 construction workers – 86 MW solar plant
The sun is burning relentlessly. In summer, temperatures of 45 degrees Celsius are not rare here. Costing around 100 million euros, one of the largest solar units in South Africa will be built on the 150-hectare site by July 2020. At times, up to 400 workers are working on construction at the same time. The posts for fixing the panels are driven 1.60 metres deep into the stony ground using a piledriver. Small detonations were even required for the distribution stations. The preliminary work for construction of the substation, office, warehouse and associated infrastructure is also already underway. It’s an adventure. Workers describe how the roaring of hungry lions in an adjacent breeding station can be heard in the morning. The fence should hold though. It’s a back-breaking job. The sun beats down mercilessly in the afternoon; snakes, scorpions and ticks lurk on the ground. Again and again, small sand cyclones move over the plant and give a taste of the harsh conditions that the solar park will have to withstand on a continual basis after commissioning. The solar panels (each 1.90 metres by 1.10 metres in size) will soon be installed. 262,000 of them equate to an area of almost 550,000 square metres. This is equivalent to 135 football pitches. The plant’s output is 86 megawatts and the electricity is fed into the public network. This is enough to supply 15,000 households in South Africa with electricity.
2.3 million metres of cable installed
The site of the solar park is on a slight gradient. A sophisticated sensor system will later control motors that can compensate for this – and can do even more. The angle of the solar panels is altered depending on the position of the sun. In the morning, the collectors are aligned at a 30-degree angle to the east. In the evenings, they’re at 30 degrees again, but this time to the west. Re-adjustment is carried out continuously. Always facing the sun. The more technology is used, the more powerful the cables and connection solutions need to be. Around 2.3 million metres of Lapp cables are installed here. A total of 36 different products are used.
Most of them are not supplied directly to the construction site by LAPP, but rather through HellermannTyton. Change of location. Back in Johannesburg, Milky Way Ave 34 in Linbro Business Park. Alan Mulder has swapped his jeans and blue shirt for a suit, white shirt and orange tie. Chad Andrews, Managing Director of Lapp Southern Africa accompanies him. Both of them are visiting the customer HellermannTyton, who have opened the door to the solar industry wide for Lapp. It’s an industry that has also become an important growth market for one of the biggest producers of electrical cable connections and components in the world. HellermannTyton is active in 39 countries and employs 5,000 workers.
Protective hose consists of a metal helix
“We have a very special relationship with Lapp,” explains Claude Middleton, Managing Director of HellermannTyton South Africa. “Their cables and connection solutions help to make our products higher quality and therefore unique.” During the tour of the production facility, Middleton grabs a cable protection hose from Lapp. The SILVYN® EMC AS-CU is a symbol of the partnership between the two companies; this partnership has stepped up over the past two years in connection with the construction of solar parks.
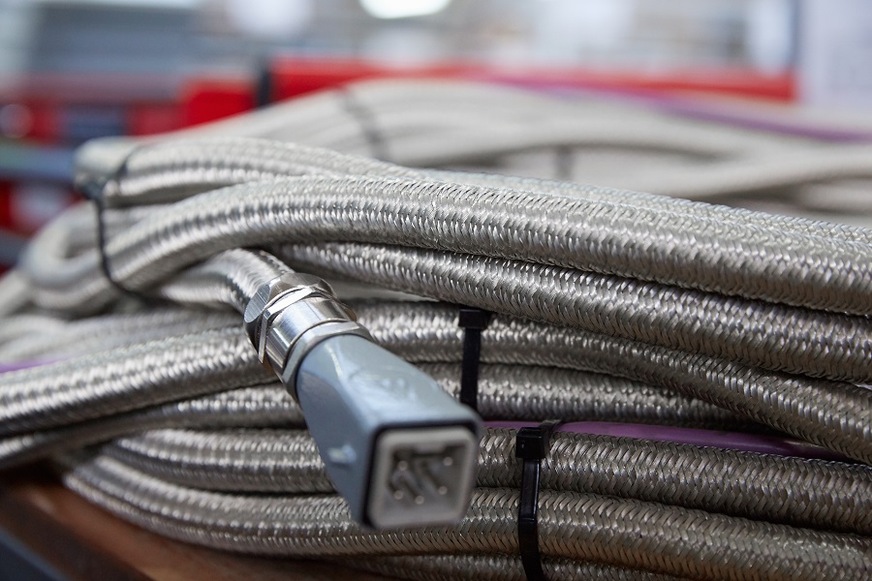
Lapp
The protective hose with a diameter of 17 millimetres consists of a metal helix which, thanks to the profiles that hook onto one another, is extremely flexible yet very resistant to external forces and mechanical movements, making it ideal to protect the solar and motor cables installed inside. They connect control boxes, each of which are 80 centimetres wide, 60 centimetres high and 30 centimetres deep and are made of steel plate, with motors and sensors. They’re little boxes of mystery, because what they contain is strictly secret. On average, 250 components are installed inside them to form a kind of “brain” that controls the plant intelligently later, and therefore also guarantees efficiency. The most important quality criterion for the SILVYN EMC AS-CU is optimum protection against electromagnetic interference.
Hundreds of fine copper wires – keep unwanted voltages away
In an extreme case, this could paralyse the entire park. Middleton explains what this means. “I’m not scared of many things, but I wouldn’t want to be at a solar park like that when the thunder and lightning hit during a summer storm,” he explains. The control technology in the distributors would not withstand the overvoltage that then briefly occurs. The SILVYN® MSK-M BRUSH nickel-plated brass conduit fittings from Lapp have hundreds of fine copper wires that ensure optimum 360-degree shielding and therefore keep unwanted overvoltages away from the inside of the boxes. “When we looked around on the market, we couldn’t find anything comparable. We construct high-quality components for the solar industry and, for this, we need the level of quality that the connection solutions from Lapp provide.” (Michael Thiem/hcn)
Part 2 of the story will follow soon.