When construction products are placed on the market, they are regulated by the European Construction Products Regulation 305-2011, which specifies essential characteristics in harmonised standards. However, as there is currently no harmonised standard for photovoltaic systems on flat roofs, the EN 1090 standard is used, which regulates the manufacture and installation of steel and aluminium structures. This standard requires every manufacturer who places a product on the market to provide a declaration of performance and label the product with the CE mark.
See also: A versatile hook for pitched roofs
However, CE labelling alone is not sufficient for the installer to be able to pass on liability in the event of damage. He must also have a structural analysis certificate and prove that he has installed the solar power system correctly and followed the installation instructions and any ballasting plans.
Damage due to incorrect default settings
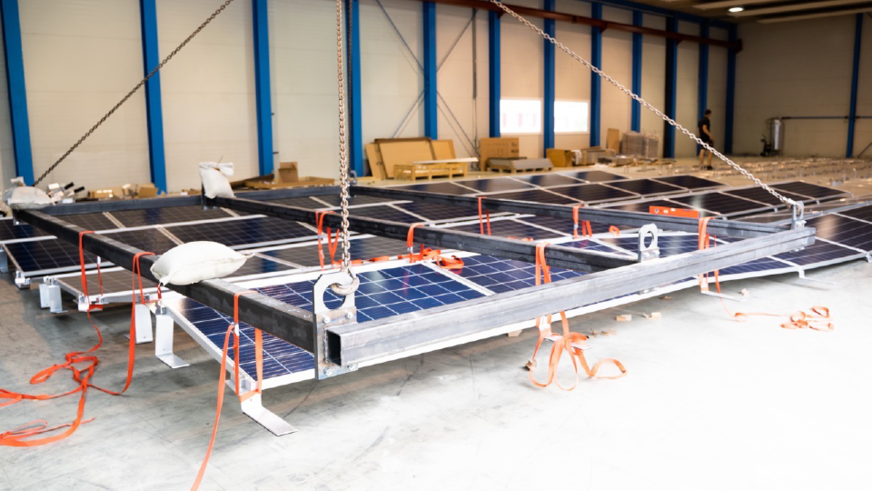
Aerocompact
The problem with this is that planning is not done from scratch every time, particularly in the residential sector; rather, the installation is simply carried out in the same manner as in similar installations. Reputable solar installers and installation companies use a PV planning tool to plan each system. If the planning parameters are entered diligently, this tool provides all the information required for an installation and generates a structural analysis that can be taken from the project report. In practice, however, many planners accept the default settings of the software or accept planning results that exceed the permissible utilisation of the components. This approach can lead to considerable damage as many manufacturers dimension components with little margin for error. In addition, weather events are becoming increasingly extreme and the conditions on site can differ significantly in some cases.
For these reasons, the Austrian mounting system expert Aerocompact has set up an in-house research and standardisation department in Aachen, Germany, which has been headed by the internationally renowned wind engineer Dr Thorsten Kray since 2021. This department is dedicated to applied research in the field of photovoltaic system statics. The team works closely with Aerocompact's in-house software department to continuously develop the AEROTOOL programme. Compared to its competitors, Aerocompact's engineers take a very rigorous approach. Since its applied research and in-house software development cooperate so closely, Aerocompact is able to strike an uncompromising balance between optimising costs and ensuring safety.
Like a chess computer
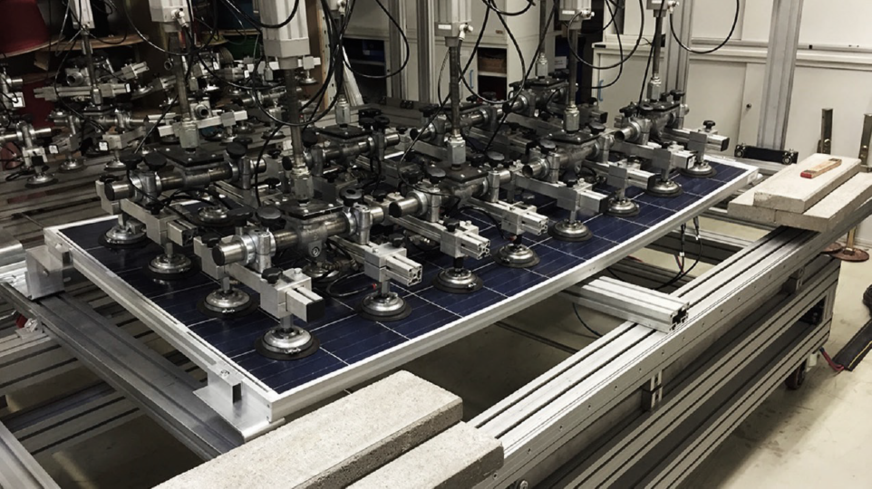
Aerocompact
The research results are first converted into mathematical algorithms. Using them as a basis, the team then programs the optimiser, which works like a chess computer and further optimises the planning result for each specific project. The optimiser not only takes into account different snow and wind loads, but also country-specific standards, building-related influencing factors and load-bearing capacities. Depending on the ballast, static verifications, wind and snow loads, etc., the AEROTOOL then selects the appropriate components in a modular and cost-optimised manner.
Did you miss this video? Christian Ganahl: Flexibly opening up more roofs for solar power
The plans are then checked by a separate department, Verification Engineering, which Aerocompact has set up for this purpose. The verification engineers are part of the software development process and are responsible for checking the defined statics in the software's programmed code. On this basis, the software quality department programmes the test automation, which automatically checks and ensures the validity of the static application every night. Every newly implemented feature is checked by the test automation. As far as we know, we are the only assembly system manufacturer in Europe with test automation.
Prepared for everything
Our aim is to cover all contingencies with our set of rules. To ensure that this works, we regularly gather feedback from our customers. From this, we learn which requirements they are confronted with and define further improvements to our software on this basis.
Thinking of investing in SOLAR? Then make sure to sign up to our free monthly NEWSLETTER!
Because we are continuously developing our AEROTOOL, planners have more options with our system. For example, they can split the loads in the event of a load limit and, if necessary, place additional anchors to further reduce the ballast. Our SN2 flat roof system alone has five different ballast positions. Since our software development department calculates the optimum solution for every situation, we are able to deliver competitive results without compromising on safety.
Optimally trained
We offer our customers a wide range of configuration options to optimise planning results and guarantee that the project planning is successful even in challenging situations. To fulfil these complex requirements, our software support team is available to our customers at all times. We have introduced a ticket system with a 24-hour response time. In addition, new licence holders receive comprehensive onboarding training.
Utilising roof surfaces, integrated lightning protection saves costs
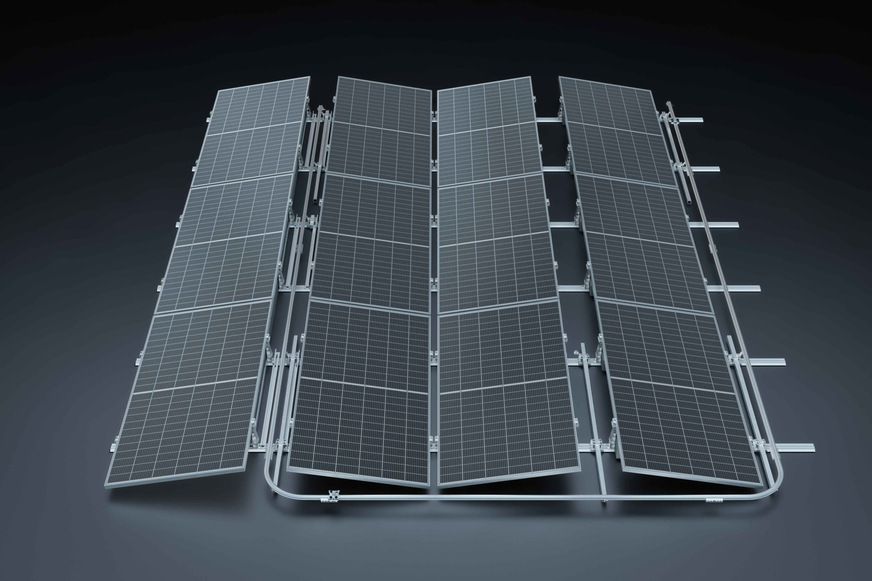
Aerocompact
While the external lightning protection is planned by specialised experts, we as a racking manufacturer ensure that our system is integrated into the lightning protection and is capable of withstanding lightning currents. When a system is correctly integrated into the lightning protection system, it must be able to withstand a current of 50,000 amps. If you want to install air-termination rods directly on a substructure, the system must be capable of withstanding 100,000 amperes of lightning current. We have tested our SN2 flat roof system for 100,000 amperes.
Also interesting: Aerocompact and Securenergy realise PV system using sandwich panels
As the cross-sections of our system are more than sufficient and meet the requirements of the applicable lightning protection standard, no further modifications are required. The external lightning protection expert only needs to create a connection from our system to the existing lightning protection. He can do this easily and conveniently with our WLC 8-10 clamp and an aluminium wire or an equivalent clamp. For our SN2 flat roof system, for example, the tightening torque of 10 Nm must be observed.
Protection against falls
For fall protection, we work together with our partner Innotech from Austria. With the solution we have developed, you can choose between a rail-based and a rope-based version. While the rope-based safety system is cheaper, the rail-based version offers more flexibility. It is important that sufficient ballast – at least four modules or 600 to 800 kilograms per module field – is available. In the case of very low wind loads, we provide additional ballast if necessary. This prevents a person from falling to the ground.
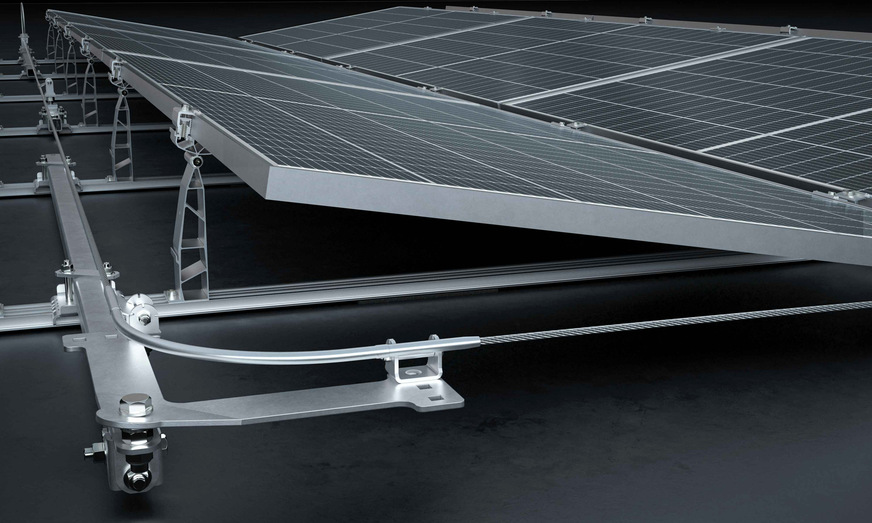
Aerocompact
Shaping the standards of tomorrow
The topic of safety is very important to us. That is why we are involved in various committees. Among other things, we are currently working with other experts on a harmonised standard for installations on flat roofs in Germany with pitches of up to 10 degrees. As head of the working group on Annex A of the standards committee for the future DIN 18199 entitled "PV and solar installations on or near roofs", our expert Dr Thorsten Kray is responsible for working out wind loads on solar installations. In addition, Dr Kray is also the main author of the Windtechnologische Gesellschaft e.V. leaflet on "Wind tunnel tests in building aerodynamics", which will be published in January 2024 and regulates, among other things, how wind loads can be measured on roof-mounted solar systems experimentally. Moreover, Dr Kray is involved in the construction technology section of the German Solar Industry Association and has contributed his decades of expertise investigating boundary layer wind tunnels on solar systems to the "Guidance paper on the design of mounting systems based on wind tunnel tests". (mfo)