To this end, the company has developed an innovative manufacturing process carried out in a single automated step. Wafer-based crystalline solar cells are combined with structured sandwich panels from 3A Composites Mobility, made of recycled PET.
The new modules are optimized for use in the automotive industry and have been installed for the first time in the trailer of the international SolarButterfly project. With a total power of 15.2 kW, they provide sufficient electricity for the SolarButterfly towing vehicle and the operation of the tiny mobile house built in with the trailer. Weighing 4.7 kg/m2, they are 55 percent lighter than conventional solar modules, yet, the efficiency of the solar cells used is 24 percent.
SolarButterfly demonstrates the feasibility of sustainable vehicle integration
Sustainable integration of photovoltaics in vehicles means reducing material consumption and using sustainable components. Both are demonstrated in the SolarButterfly project. Here, the photovoltaic modules are not additional components that are retrofitted to the vehicle. Instead, they are completely integrated and form the energy-generating vehicle shell as the Solar Butterfly, substituting conventional materials used before. Just as in the automotive industry, weight reduction by maintaining structural stability is crucial.
“On a global level, Power Production and Transportation are the two single largest emitting CO2 sectors by far. Vehicle-integrated photovoltaic is the Swiss army knife that tackles both issues right at the source. Considering the annual number of new vehicle registrations in Europe alone, the usable car, bus, and truck rooftop area can provide more than 20 GWp of solar energy. It is clear that we have to think about sustainable materials right from the start,” says OPES Solutions CEO and Founder, Robert Händel.
Achieving optimal material properties with R&D partnerships
The seamless integration of solar modules in vehicles places new demands on materials compared to those of conventional modules. Here, OPES Solutions built on previous vehicle integrated photovoltaics (VIPV) solutions that the company developed with the Fraunhofer Center for Silicon Photovoltaics CSP.
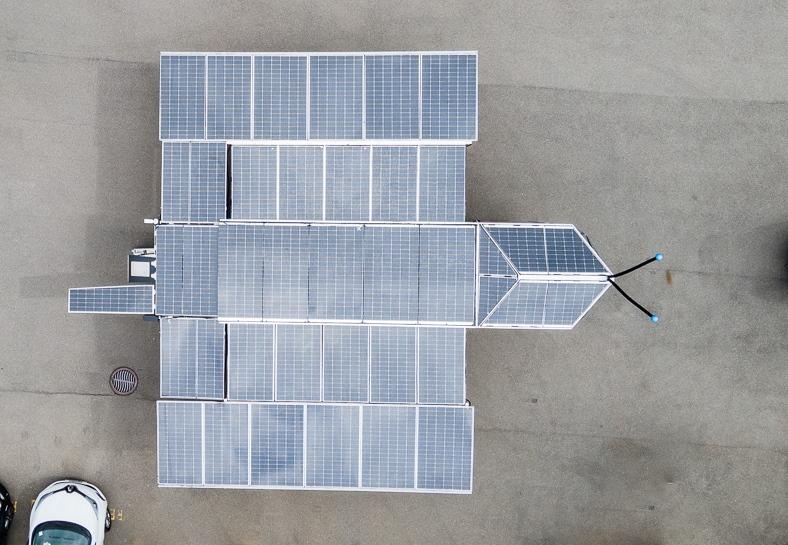
Opes Solutions
The base construction of the ocean plastic solar module is the proprietary solar technology used for Opes Solutions’ VIPV module type SolShell, which is already in production. Some of the core features are outstanding heat insulation that keeps the interior of the vehicle cool and the increased resistance to vibrations, so that the connections of the solar cells remain permanently undamaged. This is the result of extensive R&D and testing. “Our vibration testing machine worked around the clock the past few years with complete vehicle roofs, until we found the perfect solar cell embedding and interconnection technology,” Robert Händel adds.
Opes Solutions is also continuously optimizing the VIPV module efficiency. With their clustered solar cell layout and integrated by-pass diodes, the power output of the high-efficiency solar cells from Longi is optimized for partial shadow and low light scenarios. (hcn)
Did you miss that? Canadian solar racing car integrates panels from Opes Solutions