The research factory, which was rebuilt and significantly expanded in 2018, is the largest R&D center for crystalline silicon solar cells in Europe.
“We are thrilled to be able to present such outstanding results so soon after the inauguration of our PV-TEC,” said Ralf Preu, Division Director of PV Production Technology at the Fraunhofer Institute for Solar Energy Systems ISE. The laboratory operated as a research factory from its inception in 2006 until it was destroyed by fire in February of 2017. Rebuilding was completed in record time and the center reopened one year ago, providing one-of-a- kind infrastructure for industry-driven solar cell research, including research and development for processing equipment. “Thanks to the rapid rebuilding process and our innovative infrastructure and equipment, we have the opportunity to usher in the future of photovoltaics and cement our position as a leading international developer of PV technology,” added Preu.
More space for technological innovation
Fraunhofer ISE used the rebuilding process to restructure the laboratory, creating front- end and back-end divisions housed at two separate locations. The reorganization is intended to better meet the growing technical requirements for the various processes in terms of infrastructure and indoor climate, while at the same time creating space for new production lines and technologies. Today, around 180 employees develop manufacturing processes across 2400 square meters of technical facilities to make the high-efficiency solar cell concepts of tomorrow a reality. They collaborate with industrial partners from Germany and across Europe on cost-effective processes for the next generation of solar cell technology, with the aim of improving cell efficiency and energy yields, increasing throughputs in process technology and implementing current trends such as building- or product-integrated photovoltaics.
Current research is focusing on cost-effective processes for monocrystalline PERC solar cells that achieve efficiency values of more than 22 percent and can be implemented on an industrial scale, as well as solar cells based on passivated contacts (TOPCon, heterojunction), including tandem solar cell designs. Concepts for digitalizing solar cell manufacturing (digital twins, self-learning machines, predictive maintenance) also undergo research and testing for the next generation of production equipment.
Key areas of research focus
The front-end technical center, located on Hans-Bunte-Strasse in northern Freiburg, is devoted to wafer characterization, wet-chemical etching, doping and processes for surface coatings. “Our work here focuses on upscaling high-efficiency solar cell technologies and integrating automation concepts that are essential for mass production so that we can present the photovoltaics industry with ready-to-use solutions,” explains Dr. Jochen Rentsch, Head of the Department of Production Technology – Surfaces and Interfaces at Fraunhofer ISE. New techniques for quickly and carefully handling silicon wafers between process steps are also of interest, given the wafers’ sensitive surfaces and ever-increasing thinness.
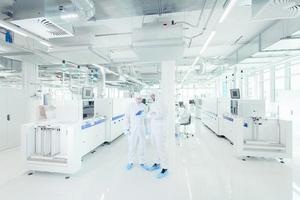
The back-end department, housed in the Solar Info Center on Emmy-Noether-Strasse, concentrates on printing and laser technologies and the characterization of solar cells. Along with fully automated production facilities, it is equipped with state-of-the-art laboratories for the development of printing and laser processes as well as the analysis of mono- and bifacial solar cells.
“A key focus of our research is developing superfine and precisely positioned contact structures in order to optimize material use in solar cell production and improve efficiency,” explains Jan Nekarda, Head of the Department of Production Technology – Structuring and Metallization.
To characterize the cells, a machine was built to perform automatic measurements of high-efficiency solar cells in various formats quickly and extremely precisely, even under bifacial illumination.
In addition to photovoltaic applications, PV-TEC develops technologies for other industries, for example coating technologies for fuel cell membranes or customized structuring processes for electronics.
Technological achievements at the new PV-TEC
Busbar-free PERC cells with an efficiency value of 21.9 percent: The busbar- free solar cell was developed entirely in-house in an industry-driven process. It is made of monocrystalline silicon with an aluminum oxide passivation layer on the rear side and a homogeneous emitter on the front side.
Bifacial pSPEER shingle solar cells with a power density of 235 W/m2 (font- side irradiation 1000 W/m2, rear-side irradiation 100 W/m2). This advance in PERC technology makes use of patented passivated edge technology to improve energy yields by combining the low-loss separation of solar cells with shingle technology, which minimizes shading on both sides of the cell.
TOPCon (tunnel oxide passivated contact) cells with 22.5 percent efficiency: The cell was manufactured using Fraunhofer ISE’s own process. TOPCon, a charge carrier-selective contact developed at the institute, is based on an ultra-thin tunnel oxide in combination with a thin silicon layer and enables excellent charge carrier selectivity. (HCN)