Although invisible from the outside, battery cells are the core components of any battery storage system. But what are the “inner qualities” of energy storage solutions? Are the battery cells interchangeable today or what features and differentiating factors should buyers take into consideration? Electrochemistry expert, AD Huang, Head of the BYD Battery-Box business, shares insights on what material, production processes and components can contribute to the safety, stability and life-span of a battery storage solution.
“When purchasing a battery storage system, buyers should of course consider factors such as the manufacturer track record, power output, warranty and compatibility of the system. On paper, most of the solutions on the market may look very similar,” explains AD Huang. “However, in my opinion it is also important to take a closer look at the battery cell itself as the core component of the system and a key factor for the system safety and reliability”.
Key factors buyers should take into consideration include:
Transparency with regards to the components
The first question to ask is: Does the system provider even disclose the components? With many brands, the buyers don’t even have the insight into what battery cells the storage systems brand is using. This is an information buyers should always ask for – because the battery cells are not only key to the performance but also an important feature for the battery safety. It is also advisable to compare the expected battery life-span. Consistency and uniformity in the production process, chemical composition, material selection, scientific proportion configuration, and strict quality control throughout the production process are all critical factors in ensuring the long lifespan of the battery.
Chemical configuration
Lithium iron phosphate (LFP) has increasingly gained ground as top choice for battery solutions as it offers a variety of benefits compared to lead-acid batteries and other lithium batteries. It is extremely stable, and the deintercalation and intercalation of lithium ions have little effect on it. Lithium iron phosphate also has a stable structure and high thermal stability and does not release oxygen at high temperatures. This is a key factor with regards to safety when compared with other materials such as ternary materials and lithium cobalt oxide materials. It is also a more sustainable and environmentally friendly solution as the production of LFP batteries consumes fewer natural resources and does not require cobalt.
Did you miss that? Pioneering energy storage solutions showcased
Battery vendors use specific LFP compositions. BYD batteries for example have a unique chemical configuration: The positive electrode uses lithium iron phosphate (LFP), while the negative electrode uses graphite. Special additives in the electrolyte ensure that the batteries offer a superior cycle life and safety. Through different proportions of the additives, different performance requirements of the battery can be achieved. The Lithium-Iron composition used by BYD has a particularly low expansion degree and a high decomposition temperature. Making it especially stable, even at high temperatures. The combination of all of these factors contribute to the excellent safety record of the systems.
Casing
The casing of the battery cells is another important factor in ensuring the longevity and safety of the system. A correctly applied high quality aluminum casing for example provides a strong corrosion resistance, a high stability and resistance to environmental challenges. Additionally, it offers good ductility and a high heat dissipation, and is lightweight. The non-magnetic property of aluminum also reduces polarization of the battery. Moreover, the material is more environmentally friendly than alternatives and can be recycled very well.
Production process
The battery production process is a crucial factor in ensuring the quality of the final system.
To ensure the highest quality level, all raw materials need to be precisely configured in a certain proportion for production. The battery production process of most tier one manufacturers is highly automated, but it also involves close monitoring to ensure high quality standards. Key aspects that are important to oversee include process control, temperature control, and other conditions. In the first phase e.g. controlling the pole piece parameters is critical. In the middle section, ensuring uniformity of the lugs, pole core thickness, and welding parameters are important. In the final stage, the restraint amount, liquid injection amount, chemical composition, and working steps must be carefully controlled as well.
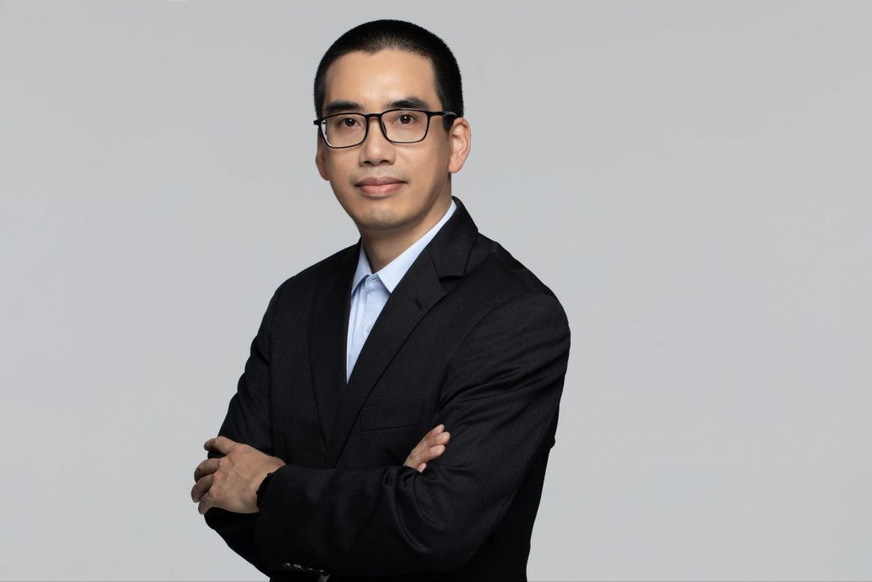
BYD
A particularly critical step in the process is the coating quality of the front section. This involves ensuring that the pole piece is even and smooth, with no defects such as material drop, lack of material, scratches, or cracks. In addition, the length of the tab and FTT welding position must be carefully controlled to ensure proper function. The subsequent formation process and formation restraint fixture are also important steps in the production process.
Vertical integration
The level of a manufacturer’s vertical integration is another factor to watch. A high integration level can be beneficial because this way knowhow and insights from different areas can be utilized within one company – connecting from product to design and manufacturing with feedback from end users and thereby influencing even the most basic elements of a system down to raw material extraction. This not only provides opportunities to improve process efficiencies but can also help to respond to market needs in the most agile way.
Did you miss that? Dr Eric Rüland from RCT Power: The recipe for success behind the HTW test winner
“The market was faced with a number of safety incidents with battery systems last year. Therefore, choosing battery systems carefully and with a critical look at quality and security factors has become key”, says AD Huang. “BYD was one of the earliest vendors to invest in advancing LFP technology for both EV and energy storage. A continuous focus on R&D and on advancing this technology even further underlines our focus on quality and safety and is one of the reasons for the track records of more than 400,000 Battery-Box systems having been installed in the market with not a single safety incident.” (A. Huang, hcn)