The market for private solar storage has only existed for five years old when the next opportunity beckons: Companies are increasingly asking for commercial-scale storage units. They are the linchpin of a commercial installation for self-consumption consisting of PV and usually a cogeneration unit or a set of fuel cells; in combination with heat pumps, LED lighting and solar car ports for the employees’ EVs.
Anyone planning to design and install commercial storage should urgently take advantage of the experience gained in the domestic sector. However, the commercial field is different from the domestic field in one key aspect: Storage units for commercial, municipal or industrial customers are usually not bought off the peg as one complete package. This is a project-based sector that is all about the efficient adaptation of cascading storage systems and about adapting the modular batteries that are being offered by manufacturers and retailers.
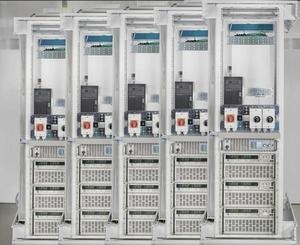
Check list is also useful for commercial storage units
The Karlsruhe Institute of Technology (KIT) is performing extensive tests of domestic storage units for safety and efficiency. The results can just as well be applied to commercial systems and its conclusions generalised. The check list for choosing domestic storage units that follows this article can also be useful for commercial storage.
The researchers at the KIT have listed their findings in a table that shows the 16 storage systems that they tested. The top section shows all of the safety-related criteria – concerning transportation and functionalities. The bottom section shows the performance-related measurements that indicate the efficiency of these systems. “The red fields mark major safety deficiencies or efficiencies of less than 80 percent,” project manager Nina Munzke explains. “Very highly efficient systems with 96 or more percent have been highlighted in green.” Three storage systems failed the test altogether: too dangerous, functional or EMC issues.
Systems usually run on partial load
Her conclusion is that the efficiency of the power electronics is most critical to the overall efficiency of a storage system. “The battery inverters tend to cause the greatest losses within the system,” she says. “Also, our assessment was that indicating the maximum efficiency in the data sheet makes very little sense. In real life, the systems tend to run on partial load.” For that reason they were charged and discharged at 50 percent of their nominal capacity, i.e. at only 500 watts. “That is closer to the real-life requirements of PV and home power supply.”
In saying this, she basically confirms an insight that has been well-known for string inverters: They also only run on partial load. Only with the sun fully shining onto the panels, during the middle of the day, do they possible achieve full load. Unless the inverters are used in Turkey or in Africa, where the sun shines relentlessly all day long.
The table also demonstrates that a storage system can end up with decent efficiencies, despite low values for the power electronics. A key factor here is the quality of the management system (response time). The criteria by which it is measured are the dead time and the setting time, which describe how fast the battery management system reacts to changes in load and how long it takes for the battery to adjust to the new load requirements.
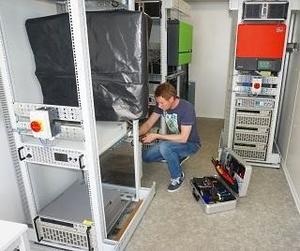
Do not underestimate standby consumption
The standby consumption of the storage units should not be underestimated. The tests just assessed the systems, rather than how it is integrated into a building. For instance, the standby consumption of a Wi-Fi router is not factored in.
The tests were anonymised, that was a major part of the project. However, the installing companies that are already involved in installing storage batteries can very easily compare the results with the operational data of the units overseen by their monitoring systems. The point is to separate the wheat from the chaff.
Tested according to defined load curves
For their tests, the KIT researchers have used the various load profiles defined in the VDI 4655, in addition to typical load profiles for private households from a research project of Vienna Technical University. “We combined both approaches and realised that the typical weather data in VDI 4655 provides for very practical load profiles,” Nina Munzke says in retrospect. “That way, we end up with reliable information on the battery and the power electronics. That works well going forward.”
In the table, the degree of self-sufficiency indicates how much self-consumption the storage unit in question managed to achieve. The field for intelligent charging strategies shows if the system was (marked in green) or was not (marked in red) equipped with one.
Higher capacities and currents
The same criteria apply to commercial storage, albeit at higher capacities and charging and discharging currents. In general, the only way that full loads are to be expected is with EVs when the charge points are connected to the storage batteries. But in that case it makes sense to include supporting generators such as a cogeneration unit or fuel cells.
After all, photovoltaics and high currents, even if only briefly, do not really go together. The only way to produce high outputs with a self-generation system is to have generators that reliably produce power. When short-term peak loads occur, it may make sense economically to take advantage of the company’s grid access.
Now that the initial safety and performance tests are complete, the KIT will analyse the long-term behaviour of the systems. “We want to find out if the batteries are showing any signs of change after a year and a half or two years,” Nina Munzke says, providing a prospect to the future. “This project will continue to run until September 2018.”
Standardisation is proceeding
The process that started with domestic storage is now continuing with commercial storage. The safety check list also applies to them, except with additional provisions on operational fire protection, emergency power and uninterruptible power supply (UPS). And they are also covered by the new efficiency check list that the industry has agreed on early this year. SMA surged ahead and tested their inverters according to the efficiency check list. The results were presented in July.
This autumn, the process of standardisation will be taken into the next round. “Manufacturers have been given the specifications they need to pre-test their systems. The standards in terms of accuracy of the tests and metrology are very exacting,” Tjarko Tjaden, researcher at the Berlin University of Applied Sciences (HTW), explains. He is a member of the research team headed by professor Volker Quaschning and was directly involved in writing up the guidelines. He goes on to say: “Because the tests were developed in concert with the manufacturers and institutes, and with an eye on practical considerations, they already are widely accepted.”
Check list is a first step
The check list provides reproducible guidelines for the tests. It was first developed for domestic storage batteries, but has general standards that also apply to commercially used units. Researchers and manufacturers spent two years working on the check list. “Now we will have to take the normative route,” Tjaden says, looking to the future. “It will be about developing testing standards and standardising the information provided in the data sheets of storage systems.” So far, the check list has been based on the data provided by the manufacturers, which is practically un-verifiable.
Currently, the data gathered from online monitoring portals of the manufacturers is inaccurate, not precisely defined and thus hard to compare. It is often not at all clear, how much energy is wasted by the power electronics or the management system of the battery. Losses due to standby, possibly including the Internet router, are very different for the various systems – depending on how they are integrated into the building. In addition to the systems technology, integration into the building and the household supply is a major factor determining the efficiency of a storage unit.
So far, the check list on efficiency of storage is based on a voluntary commitment by the industry. At the Intersolar and the EES Europe in Munich some suppliers indicated a willingness to meet these new requirements. But once they become the test standard and are issued, for instance, by the German Commission for Electrical Engineering (DKE) and the VDE, they are considered state-of-the-art and thereby gain a certain authority that it will be hard to avoid.
Long service life as the most important goal
The key criterion for the efficiency of a battery is its service life. So far, the currents allowed for charging and discharging, the depth of discharge and the number of cycles per year are controlled to protect sensitive lithium cells from overheating or overvoltage, in other words: to go easy on them.
But in the end, the result is all that matters. And when it comes to storage batteries, matters are no different. Private as well as commercial customers’ concerns eventually come down to one question: How much does one kilowatt hours of solar power after it has been stored in the battery and taken out again and used?
Simulations have shown that for AC-connected system in particular the real-life operational behaviour is relatively simple to show. “This allows us to make reliable predictions on the average efficiency of AC-connected systems over the year, based on measurements stipulated in the efficiency check list,” Johannes Weniger, co-researcher of Tjarko Tjaden at the HTW in Berlin, explains. “We want to provide a simulation-based indicator to make the efficiency of differing system designs comparable.” A process of validation will still have to show whether it is possible to apply such simulations to DC-connected systems in a sensible manner and at the required precision.
How to simulate intelligent charging strategies?
It is a complex issue: Not only do the losses due to standby over the course of the year have to be factored in, but also efficiency of the system control, the use of forecast data, the system control’s behaviour in terms of dead time and setting time, limiting the feed-in output at the point of connection to the grid and the AC loads in the building. “This needs to be resolved at one-second intervals in order to obtain reliable date,” Johannes Weniger says. “Our simulations have already shown that limiting the feeding in to 50 percent can significantly alter the efficiency of a battery system – given that it operates without forecast-based charge planning.” (Heiko Schwarzburger)
Read more about energy storage systems.
Stay informed, get our free newsletter twice a week, register here.
More useful information:
https://www.pveurope.eu/solar-storage/solarwatt-and-fronius-train-new-installation-partners-uk