The Centre for Solar Energy and Hydrogen Research Baden-Württemberg (ZSW) is working on this in a research network. Partners are the Fraunhofer Institute for Chemical Technology ICT, the Fraunhofer Institute for Manufacturing Technology and Applied Materials IFAM and the Fraunhofer Institute for Material and Beam Technology IWS.
The project is called “KontElPro” and has been allocated a total of around 1.8 million euro in funding by the Federal Ministry of Education and Research (BMBF) as part of the research cluster “Intelligent Battery Cell Production” (InZePro). The demand for batteries is increasing all over the world.
They are a key technology for various fields, such as electromobility, but most batteries still come from Asia, with just a few of the battery cells for today’s electric cars being produced in Germany. In a bid to change this situation, the Federal Ministry of Education and Research has reviewed funding for battery research.
Milestone for battery production in Germany and Europe
The joint research work is a major milestone for battery production in Germany and Europe on the way to smart, environmentally-friendly, space-saving and resource-efficient electrode manufacturing processes. The majority of battery electrodes and battery cells have been manufactured in Asia until now. It is an energy-intensive process in which an electrode paste is applied to a thin metal foil and the toxic solvent is drawn off in a long furnace.
The approach in the “KontElPro” project is different, however, in that the focus is on solvent-free electrode production using extrusion followed by dry transfer processes. No toxic substances are used in this case and energy-intensive drying processes are not part of the process chain either. This makes it a win-win situation for the environment and health.
Did you miss that? DLR develops cobalt-free batteries for electric vehicles
Artificial intelligence (AI) is the basis for optimising the new manufacturing process. The AI-powered process control technology also saves time, energy and costs. Artificial intelligence is therefore opening the door to a cost-effective and environmentally-friendly manufacturing process for electrodes for battery cells in the future.
Develop a self-learning AI model
The ZSW in Stuttgart will develop the self-learning AI model for the optimisation and control of the individual processes and the overall manufacturing process in electrode production for battery cells. “The ZSW has been doing research work in the field of AI and machine learning for more than 20 years. We can contribute our expertise in applying methods and our know-how for even more sustainability in the energy transition,” explained Maike Schmidt who heads up the System Analysis department at the ZSW.
In this project, the Fraunhofer IFAM is working on monitoring and controlling the extrusion processes for the continuous production of battery components. The dry transfer systems for solvent-free battery electrodes are being developed by the Fraunhofer IWS, with monitoring and control functions forming part of the brief for this process. The Fraunhofer ICT is developing and programming a database to collect the process data and providing the interfaces for AI development.
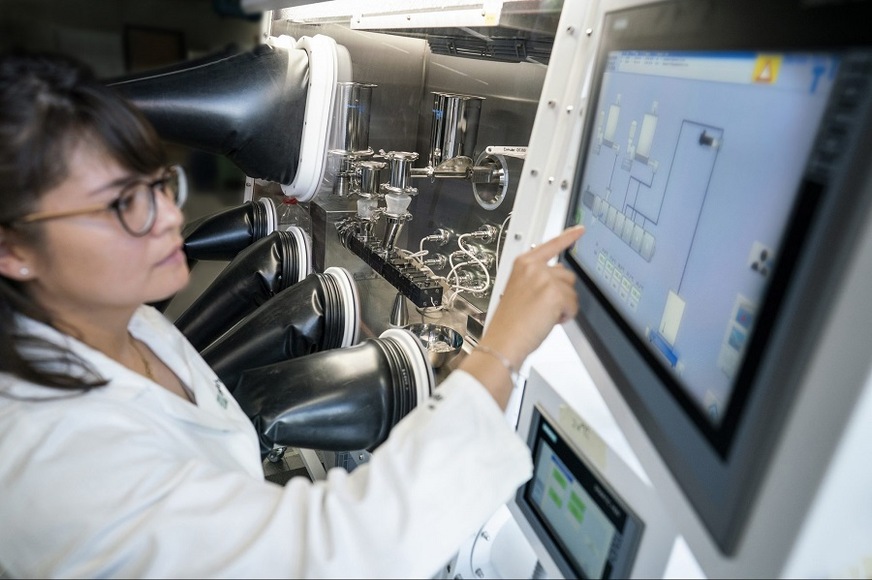
Fraunhofer IFAM
At the same time, the established processes are to be expanded to include an AI-based in-line process control and a database networked across sites. The aims are to evaluate data automatically and to model, optimise, control and monitor the processes with AI support. Where irregularities arise in the processes, the AI will intervene directly in the control system and make the necessary adjustments to ensure homogeneous and optimum electrode quality throughout.
Ensure consistently high quality of the battery electrodes
“The latest AI methods allow us to record, evaluate and control all the main factors influencing the quality of the electrodes during production and so ensure a consistently high quality of the electrodes over the entire process,” explained Anton Kaifel who heads up the AI and Machine Learning team at the ZSW. (hcn)
Did you miss that? Boom in utility energy storage demand drives advanced battery research